
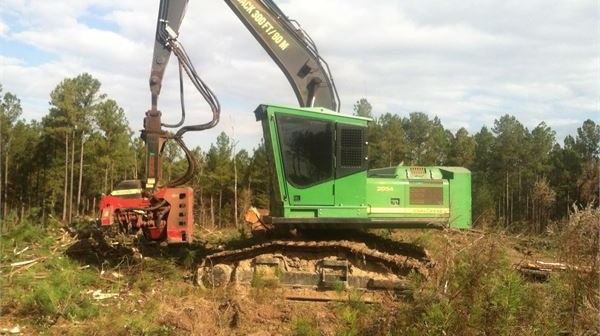
Suitable Steep Terrain Forestry Equipment

According to the BC Forestry Safety Council, “Operating logging equipment on steep slopes increases the likelihood of reduced machine stability that can result in an upset or roll-over”. Due to the instability of steep slopes, serious injuries or fatalities can occur to workers, resulting in expensive lost production and machine repairs. This event can also cause significant environmental damage.
Since worker safety is a paramount concern among business owners in the forestry industry across the globe, they are constantly looking for methods to protect their employees while increasing harvest yields. For this reason, they look to various types of heavy harvester forestry vehicles for cut-to-length logging operations, felling, delimbing and bucking trees.
The forest harvester was primarily developed in Sweden and Finland. This piece of equipment is used almost exclusively in these countries for commercial felling. Wikipedia states that the first fully mobile timber harvester was introduced in 1973 by Finnish systems engineer Sakari Pinomäki, who owned PIKA Forest Machines. The first single grip harvester head was introduced in the early 1980s by the Swedish company SP Maskiner. Both of these machines are used in the harvesting of plantation forests throughout the rest of Northern Europe.
Harvesters are used in both level to moderately steep terrain for clear-cutting large areas of a forest. Clear-cutting refers to the practice in which most or all trees in an area are uniformly cut down. In terrain where there are very steep hills for removing individual trees, forestry workers may use chain saws as an alternative method for cutting down trees. In parts of northern Europe, smaller and maneuverable harvesters are an alternative to the bigger machinery for thinning operations.
Manual felling is only employed during extreme conditions, such as where the tree size is greater than that capacity of the harvester head. Since forestry work can be dangerous, the principle idea behind mechanized logging of “no feet on the forest floor” is that no worker is exposed to unnecessary danger. Keeping workers inside the vehicle’s driving cab provides a safer environment and more comfortable working condition for industrial scale logging.
All harvesters are constructed on a heavy duty all terrain body. They are built as different types, such as wheeled, tracked or a walking excavator. The harvester’s body may be configured for providing tight turning capabilities around various obstacles found in the forest. They are powered by a diesel engine that provides power using a hydraulic drive for both the vehicle and the harvesting mechanism.
At the front of the harvester is an extendible boom (arm) that is similar to an excavator that enables the harvester to carry the harvester’s head. Some harvesters are variations of excavators while others are all purpose vehicles. There are some machines that are combinations of functions that allow for felling capabilities of a harvester with the carrying capability of a forwarder. This type of vehicle allows a single operator and machine to fell, process and transport trees.
According to the website Logging-On Newsletter, FP Innovations produced a report that reviews tethered logging equipment used across the world. The review discusses the steep slope handling capabilities of modern machines that are greater than the limits currently contained in safety codes.
The report provides an example of many felling machines that can operate on 60% slopes, while the current B.C. regulations restrict ground-based logging equipment to 40%. It goes on to discuss a method by which increases in the slope handling capability of logging machines can be attained by tethering them using a winch and cable to anchors, such as stumps or stationery equipment. This method can improve the machine’s stability, traction and mobility and reduce soil disturbances.
As with equipment that is used in other industries, the machines that are manufactured for the forestry industry have evolved over the years, such as the harvesters that manage steep slopes. However, the stability of the machines depends on how the equipment is constructed as well as the integrity of the trained operator for providing safety and performance in hazardous conditions.