
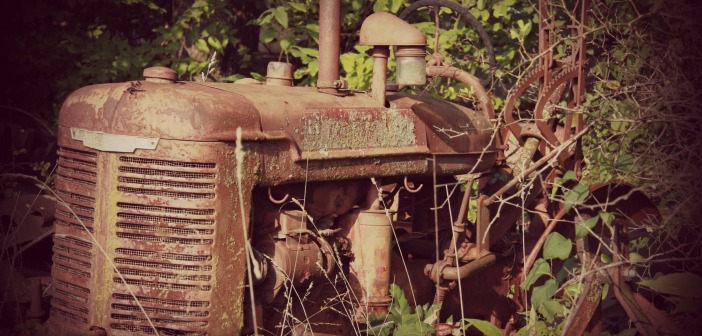
What You Should Know About Keeping Your Equipment Healthy

When it comes to servicing there’s a simple rule that you need to remember…. “Repair before breakdown will always save you money”
A regular servicing schedule is a crucial element to owning and operating heavy equipment. A solid plan will improve productivity, reduce downtime and most importantly, increase resale value.
Below we discuss the best ways to keep your equipment productive through preventative and planned maintenance.
Preventative maintenance
Fluid level checks
Before each use, it’s recommended the operator performs a check of the fluid levels. This includes coolant, oil, hydraulics, and any other fluids used by the equipment. It’s also important to check that the gauges correspond with the levels.
Keeping it clean
Not only will keeping it clean improve the productivity of your equipment, it will also ensure you can operate it safely. Thorough cleaning is almost as good as an inspection because you’re up close to all moving parts. It’s usually at this point when you’re most likely to spot failing parts or leaks early. In addition, cleaning helps prevent corrosion and keeps all warning and operating decals fully visible.
Daily inspections
If you don’t have time to frequently clean the equipment then a daily walk around is a good alternative. Usually your owners manual will have a section inside explaining what to look for in the daily checks but more often than not you’re trying to identify:
Leaks
Look for oil rings or accumulation of dust in the upper part of cylinders. Leaking cylinders will pull dirt and dust up into the cylinder, potentially contaminating the whole hydraulic system.
Hose rubs
Hose rubs are a leading cause of ruptures. They can cause spillages and loss of control. Use brackets, tape or another sacrificial covering to re-route and protect hoses.
Abnormal sounds
Listen for uncharacteristic noises when you start the machine up. If air gets into the hydraulic system (aeration or cavitation) you’ll notice a loud banging or knocking noise as it circulates through the system.
Lagging performance
Because actuator speed is determined by the hydraulic flow, a loss in operating speed is usually the first sign of hydraulic issues. Proactively monitoring cycle times is a good way to detect issues before they develop.
Smoke
Smoke from the engine could be caused by a number of things, so it’s important to make a note of the circumstances so that you can check with your mechanic. Things to look for include:
– Is the smoke blue / white?
– Does it happen on startup only?
– Is the engine cold when it happens?
Commonly these problems are related to faulty glow plugs or leaking injectors, but it’s important to get it looked at as soon as possible.
Dry linkage
Look for any dry or stiff parts that require lubrication.
Tire pressure
Check the levels are right for the conditions you will be operating in.
Scheduled maintenance
Planned maintenance program
Scheduled maintenance programs vary largely based on the type and condition of the equipment you own. As a good rule of thumb, most machinery should be serviced on a quarterly basis or every 500 miles. During this inspection the technicians should change the hydraulic, oil, fuel and air filters, and carry out visual inspections.
On an annual basis or at the end of each season, a more comprehensive inspection should be conducted by a professional. During this inspection fluids are completely replaced, hydraulic pressures are checked and cycle times / power outputs are tested etc.
Fluid analysis
Often referred to as the ‘blood test’ for heavy equipment, fluid analysis is an integral part of a scheduled maintenance program. Put simply, these tests examine a sample of oil from the engine, hydraulics or powertrain and then check to see if they’ve been contaminated in any way. The analysis will detect metal particles, water, fuel and other substances enabling you to pinpoint any problems before they develop.